IN THE NEWS
MORE NEWS

Hospitality management students gained real-world experience as they planned and executed the A Night at Awaken gala.

Barefoot on the Mall is an ECU tradition that takes place on the last day of class and offers students a chance to relax.

Ronnie Barnes will be the keynote speaker at East Carolina University’s spring commencement ceremony.

ECU recognized the hard work of its faculty members at the 2023-24 University Teaching Awards ceremony.

East Carolina swept the weekly American Athletic Conference baseball awards for the second time this season as junior outfielder Ryley Johnson and junior RHP Trey…
PIRATE PROFILES
CAMPUS SNAPSHOT
Explore ECU through the lenses of our university’s photographers.
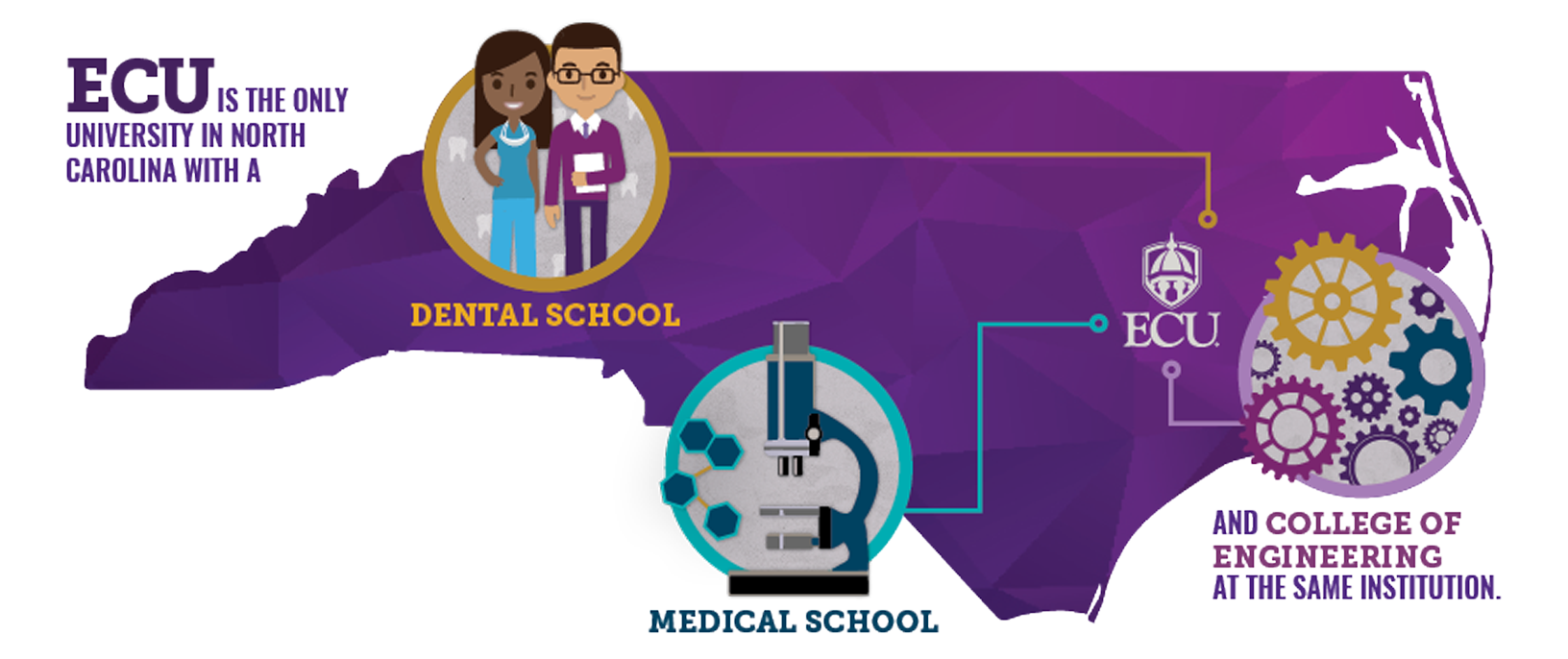
May
03
May
27